Hamson Partnership
Case Studies
Client Name: East Sussex County Council | |
---|---|
Location | Bourne Primary School, Eastbourne for 480 Year 5 to Year 11 pupils |
Project | Replacement of the entire existing heating plant and heating system while the school remained open and operational. |
Project Works | The works covered the replacement of the school’s existing heating systems in two, two storey classroom blocks. The North Block heating system was an original 1950’s one pipe variable temperature circuit serving cast iron sectional radiators. The South Block heating system was a 1970’s two pipe constant temperature circuit serving a mixture of fan convectors and cast iron radiators. Where appropriate some existing radiators remained within circulation areas and toilet areas and received weather compensated water temperature. The Classrooms and teaching areas had their heat emitters removed and replaced with ceiling mounted hot water radiant panels. These radiant panels are grouped into fourteen heating zones, with each zone being fitted with a 3-port control valve to regulate their appropriate zone temperature. The new heating system was provided with weather compensated variable temperature heating water from the new heating boilers. Hence all the heat emitters are compensated for the prevailing outside air temperature, while the classroom air temperatures are additionally modified for the number of children in the classrooms, their activity and any additional heat gains in the classroom due to heat emitting equipment or sunshine coming through the windows etc. The existing heating plant in the confined Basement Boiler Room, under the North block, was replaced with new planet plus the addition of new sealed system water expansion vessel and a heating water treatment unit. The existing control panel was replaced to achieve the heating zonal temperature control and existing hot water temperature control. These works were carried out continuously during school hours and during the school holidays by using a mobile classroom unit sited in the playground ready to take two classes for four days each on a classroom-by-classroom decanting basis while their the classroom’s had their pipework and heat emitters removed / adapted and their new radiant panels fitted. The hot and cold water systems remained as they were. The existing HWS calorifiers were fitted with new primary temperature 3-port control valves. |
Project Value | Approx £270,000.00 |
Duration | 20 Weeks |
Completion | September 2008 |
Client Name: Daily Mail Group World Media | |
---|---|
Location | Ideal Home Show 2008, Earls Court |
Project | Eco-Home for the Future |
Project Works |
Design & Project Manage the delivery of an innovative, off-site manufactured building system. This comprises a component system of prefabricated building elements to be the central feature of Hall 2 for the Ideal Home Show 2008. The primary components comprise an exposed steel frame which supports timber roof cassettes. Floor cassettes are hung from the roof by engineered steel ties. Wall panels complete with doors, windows and internal finishes tie the roof and floor components together forming the weather proof and air-tight envelope. The structure offers a winning combination of sustainable features, designed to provide low or zero carbon living –
|
Project Value | £300,000.00 |
Duration | Concept – Construction 5 months, 5 day building timeframe for Show |
Completion | April 2008 |
Client Name: East Sussex County Council | |
---|---|
Location | The Canoe Centre, Seven Sisters Country Park, Exceat, Seaford, East Sussex. |
Project | The replacing of a defective cesspool with a conversion unit and reed-bed sewage treatment system with Consent to Discharge 1.5m3 per day. |
Project Works |
The waste treatment reed-bed systems was constructed in two parts: Part 1 – A packaged MANTAIR™ conversion unit was fitted into the existing cesspool, pumped air supply. This unit was powered by a small air blower located in a small housing. The blower is provided with a 240v electrical supply and was connected to the conversion unit by a small bore MDPE pipe concealed underground. The blower provides the air that is required for the treatment process and to lift the treated effluent to the reed-bed. Part 2 - The effluent flowed into a 12m long x 8.5m wide purpose constructed wetland secondary treatment horizontal flow reed-bed planted with Common Reed (Phragmites australis). The outlet from this reed-bed discharged directly onto the surrounding wetland landscape as clean effluent. Effluent entry and discharge sampling points are fitted in the reed bed for monitoring the bed’s performance. The installation was designed to comply with the requirements of the Environment Agency PPG4; Building Regulations Section H Drainage and Waste Disposal and BS 6297:1983 requirements. |
Project Value | Approx Costs £19,000 |
Duration | 6 Weeks |
Completion | August 2006 |
Client Name: ESCC | |
---|---|
Location | Seaford Head Community College, Arundel Road, Seaford, East Sussex. |
Project | Re-cladding the swimming pool enclosure and DDA improvements. |
Project Works |
Hamson Partnership was instructed to provide Building Surveying Consultancy Services in relation to the re-cladding of the existing swimming pool enclosure and to incorporate improvements required under the Disability Discrimination Act 1995. The original pool enclosure was constructed from an aluminum portal frame clad with lightweight GRP sheeting. Whilst the frame to the building was considered to be in good condition, a number of defects were found with the original cladding, some of which were inherent to the form of construction;
The available budget would not extend to the complete replacement of the building and restrictions with the loading capabilities of the existing frame limited the available cladding options. In consultation with Structural Engineers, Stephen Wilson Partnership, a Rigidal insulated aluminum cladding system was used which successfully addressed all of the issues experienced with the original cladding, whilst being within the client’s available budget. Alterations were also made to create improvements to the signage, accessible entrance and ramped and stepped approaches. |
Project Value | £206,000 |
Duration | 12 Weeks |
Completion | April 2006 |
Client Name: East Sussex County Council | |
---|---|
Location | Battle & Langton School, Battle, East Sussex |
Project | Pitched roof replacement, including temporary roof covering |
Project Works |
Aluminium standing seam roof system carried out over 2 phases to replace a failed ‘delta’ tiled roof in a conservation area and overlooked by Battle Abbey. Phase 1 - To produce documentation for the project and execution of temporary works including Planning Supervision. In the autumn of 2002, Hamson Partnership were commissioned to provide a temporary, water tight roof covering, to the south facing elevation of the school’s main roof. This to be followed by a permanent solution once consideration of materials, detail design and Planning Approvals had been completed. The condition of the existing roof covering and internal decorations were inspected. The design was to strip the roof covering and install 3 layer insulation overlaid with a 19mm plywood decking covered with a 2 layer felt. Hamson Partnership were concerned with the low pitch of this exposed roof, and the constant water penetration apparent since its original construction in 1987. It was also understood that the roof tiling was stripped and replaced with new under lining felt within the previous 3 years. There was also the issue of uncovering a ‘difficult’ roof in the winter period. The works were carried out by J H Payne and successfully completed by the Christmas Break of 2002. Phase 2 - To produce a JCT Minor Works Contract based on Phase 1. Hamson Partnership were to design a new roof covering to be approved by the Planning Authority. Consideration had to be given to replacing the existing ‘failed’ roof tiles with a lighter material, or alternatively to omit the ‘Delta’ tile in order to break the vertical bond. This however would have required strengthening the top rafters to the existing roof truss. A structural assessment of the existing roof truss elements was carried out to ascertain the loading capability with regards retaining the ‘temporary roof’ and the proposed new waterproof covering. Consideration had also to be given to the position of the ‘Velux’ roof lights with regard to the new roof line, this required lifting the roof lights completely, together with a suitable weathering detail. In addition redesign of the rainwater goods was required to take account of the revised position of the roof covering and help alleviate the overflow situation noted on site. To complete the project it was necessary to replace water damaged ceilings and redecoration to all affected areas. Due to the low pitch and distance between ridge and eaves, an aluminium ‘Standing Seam’ system was devised, this ensured that there were no external fixings and the temporary roof could remain in-situ as a waterproof membrane, with the advantage that the light weight structure did not require any additional strengthening of the existing supporting roof members. The works were carried out by Quadric Limited and successfully completed by the end of the Summer Break of 2004. |
Project Value | £113,000.00 |
Duration | 8 Weeks |
Completion | September 2004 |
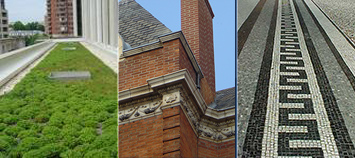

Contact Us
HAMSON Partnership Limited
Hayworthe House
Market Place
Haywards Heath
West Sussex
RH16 1DB
T: 01444 453364
F: 01444 456144
Enquiry Form
If you have an enquiry regarding the services provided by Hamson Partnership, please fill in our enquiry form.
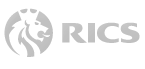
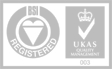